Many of today’s technologies, from the sophisticated to the mundane, rely on critical manufacturing performed in a controlled environment or cleanroom.
These cleanroom environments are required to control contamination to an extent that enables production of contaminant-sensitive products at scale. Once the domain of only the most advanced production processes on the planet, contamination control has evolved and grown to be an essential science critical to maintaining the quality of products we use every day, from our computers and cell phones to the cars we drive and the drugs and medical devices we depend on to keep us well. The tree of contamination control has many branches, but is rooted in understanding the importance of cleanliness, the various sources of contamination, and effective strategies for contamination control and removal.
Cleanliness in Controlled Environments
Cleanrooms are specialized environments where slight deviations in operation or cleanliness can impact product quality, yield, performance, and in the case of pharmaceuticals, patient safety. The cleanroom environment, including its HVAC and filtration systems, room design and layout, material and personnel flows, and personnel management are all integral to contamination control. Variations or deficiencies in these factors can lead to significant quality issues, emphasizing the need for a well-maintained and properly managed cleanroom.
Regardless of the specific type of cleanroom environment (microelectronic, life sciences, pharmaceutical, industrial, etc.) the fundamental requirement is to understand the contaminants and their behavior in order to understand and implement appropriate and effective means of control. Understanding the types of contaminants – particles (viable and non-viable), fibers, residues, coatings, gasses, etc. – is vital for devising effective cleaning strategies. While every industry and application has unique challenges and requirements, the most common types of cleanroom contaminants are particles, fibers, and residues. In developing a general strategy for contamination control, considering the risk posed by particles (whether inert, nonviable particles or microorganisms) is fundamental and useful.
Understanding Contamination and Its Sources
Particles (and related fibers) range in size from those easily visible, to fractions of a micrometer (“micron”) invisible to the unaided eye. Understanding the size and behavior of these particles is crucial for effective removal. Perhaps not surprising, the most significant contamination source in most cleanrooms is human activity. This reality underscores the importance of effective contamination control measures including facility engineering controls, personnel garbing, and control of personnel behavior - highlighting that when cleaning the cleanroom, we are usually cleaning up after ourselves. The challenge then is to effectively and consistently clean the cleanroom of something we can’t even see!
The Science of Particle Adhesion and Removal
Particle adhesion to surfaces is influenced by several factors, including gravity, electrostatic forces, van der Waals forces, and hydroscopic forces. The latter, involving a minute liquid layer between a particle and a surface, is particularly significant in cleanrooms. Effective cleaning methods must overcome these adhesion forces to ensure thorough particle removal and reliable contamination control.
A Comparative Study of Cleaning Techniques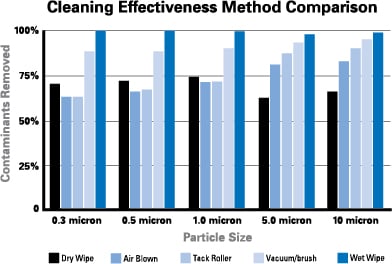
In a study comparing methods of removing particles from surfaces, it has been shown that not all methods are equally effective. For instance, dry wiping is only moderately effective, while methods like air blow-off and tacky rollers show varied results based on particle size. Vacuuming with a brush attachment can be surprisingly effective, but the most effective technique identified is using a wetted, non-shedding wipe, which removes nearly 100% of contaminants measured. Using the most effective tool for contaminant removal is critical.
Practical Considerations and Techniques
Effective contamination control however involves more than just the right tools; it requires proper techniques and consistent application. Techniques like the pull and lift wiping method and overlapping strokes when wiping or mopping are crucial for ensuring comprehensive cleaning. A methodical approach, such as cleaning difficult-to-clean features within the cleanroom first, followed by cleaning broad surfaces with appropriate tools is important for maintaining a cleanroom that is consistently in control with the least amount of variation and effort.
Contamination control in cleanroom environments is a complex but crucial aspect of manufacturing high-quality products. Understanding the nature of contaminants, their adhesion mechanisms, and the most effective methods for their removal is key to maintaining the integrity of these controlled environments. Adherence to well designed cleaning protocols, consistency, and attention to detail are the pillars of successful cleanroom cleaning and contamination control.